Share This Post:
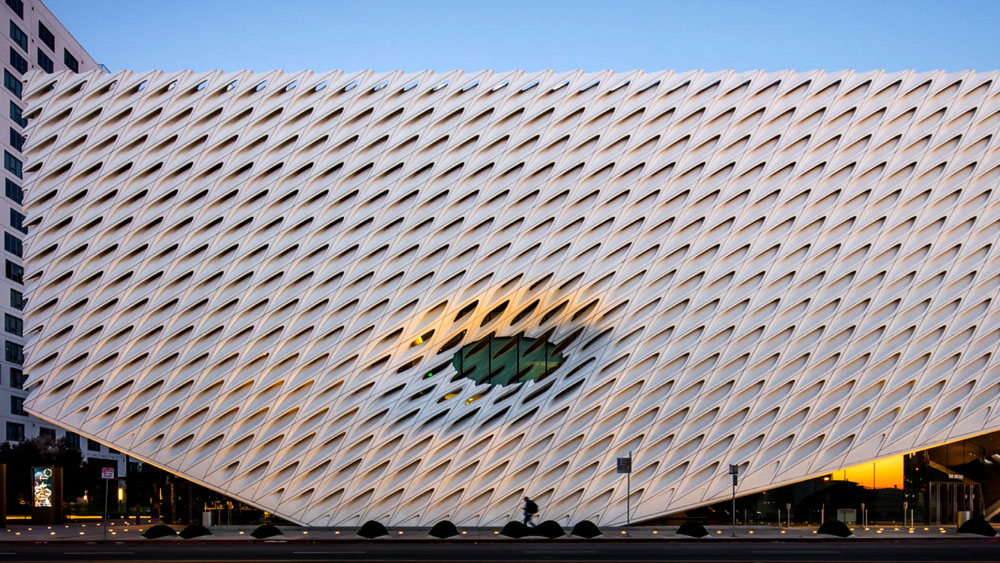
Image Credit: The Broad
Cement Just Got A Makeover
Cement Just Got A Makeover
CONSTRUCTION | Carolyn Feinstein | July 03, 2020
CONSTRUCTION | Carolyn Feinstein
July 03, 2020
Here is some great news - You can now have concrete in your foundation, driveway, walls, wherever, that is partially comprised of recycled glass! Wait, before your eyes glaze over, let me share with you why this matters.
The American Society for Testing and Materials (ASTM) has released a standard for replacing a portion of Portland cement with recycled glass. ASTM C1866 has stated that cement can now contain up to 40% recycled glass (referred to as "ground-glass pozzolans") in Portland cement.
Let me back up and tell you why this is exciting news. Cement, often referred to as Portland cement, is a very fine powder mostly made up of a clay, silica sand, and limestone. This powder can then be mixed with sand, gravel, or other aggregates to create the mortar between the bricks on your house and the concrete that was poured for your foundation. Think of cement as the glue that holds concrete together. Great stuff, sort of.
According to the UK-based think tank Chatham House, cement production was responsible for approximately 8% of the world's carbon dioxide emissions in 2017. In 2019, 90 million tons of Portland cement were produced, resulting in approximately 90 million tons of CO2 emissions. Additionally, alternative replacements, like fly ash, are produced from non-renewable energy sources (think coal-fired plants) and may introduce heavy metals into the concrete.
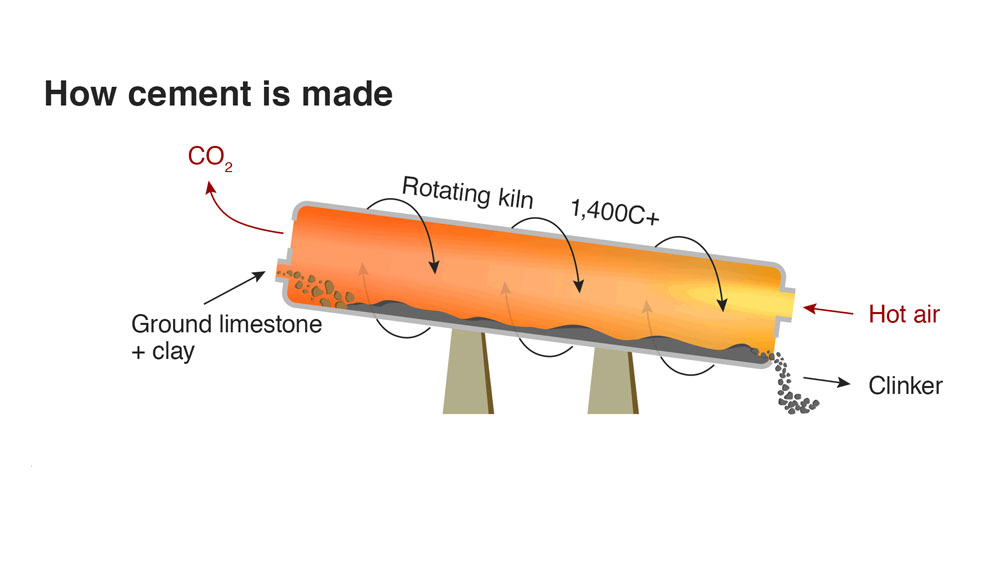
Image Credit: Chatham House - BBC
To make Portland cement, limestone, clay, and either iron ore or ash are put into a giant cylindrical kiln and heated to 2,640° Fahrenheit. The heat and rotation of the kiln split the material into calcium oxide and CO2. That calcium oxide product that comes out is referred to as "clinker", which is the base that is mixed with limestone or gypsum to form what we have come to know as Portland cement. Clinker, along with thermal combustion, accounts for 90% of the cement sector's CO2 emissions.
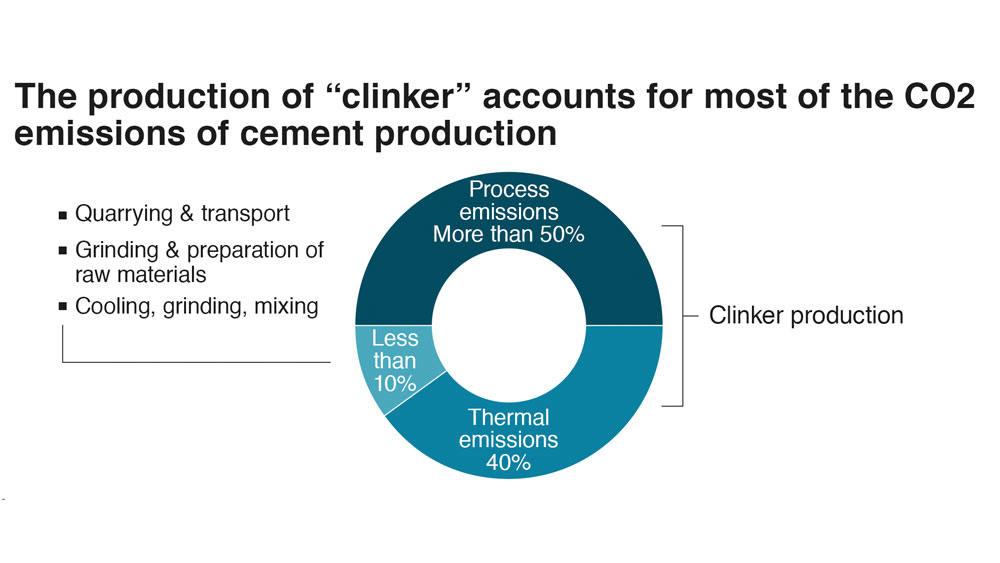
Image Credit: Chatham House - BBC
What has just been specified in ASTM C1866 is to take away 40% of that clinker and replace it with a fine powder made from recycled glass. That means up to 40% less clinker would need to be produced, and therefore, 40% less CO2 production. The substitution of ground-glass is not required, but the introduction of the ASTM standard encourages the opportunity to reduce raw material mining and CO2 production.
This is a massive step forward for construction in general as well as green building practices. We love our concrete structures. It's a versatile material that is strong and long lasting. We have created everything from great architectural works of art to bathroom accessories using cement.
While we love cement and concrete, we need to realize that these products are produced from finite resources and carry an environmental cost. So it is encouraging to see studies stating substituting 20%-30% traditional aggregates for recycled ground-glass has been shown to result in a product with increased compressive strength when monitored over a one year period. We are improving the safety, longevity, and stability of a widely used construction material, while lessening its environmental impact.